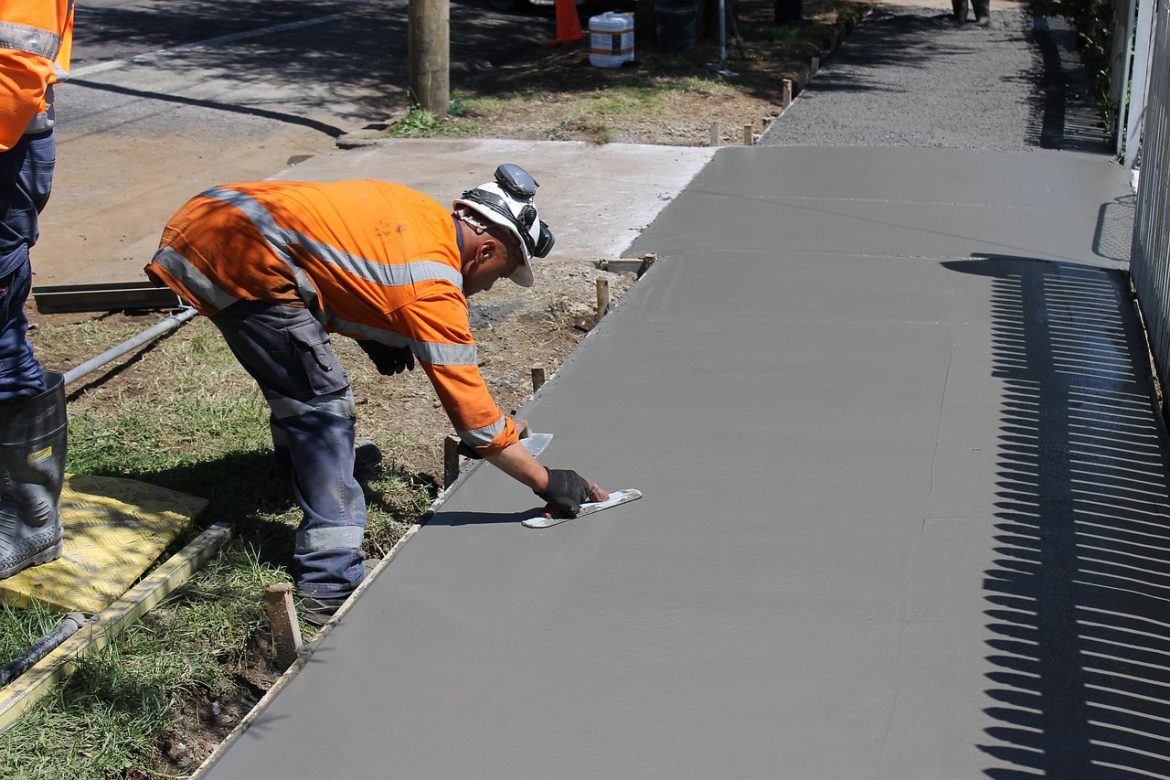
Foam Concrete
Foam concrete is a light weight type of concrete mainly use for filling works to achieve the desired level of finishing. This building material is very useful and ideal to use for roof decks, stain pan fill, elevated or raised floorings and overlay on existing floor decks. It can also be used as a light weight platform, curbs, down spout, gutters, balconies, floors, fish ponds or any other work that normally done with standard weight concrete.
Depending on the mixture and its applications, the density is ranging from 300 to 1600 kg/m3 with minimum compressive strength of 2 MPa or 20kg/cm2. It can be achieved by mixing liquid cement grout or sand cement grout by a foam made by a foaming agent. The foaming agent is as per the supplier properties and specifications.
Density (kg/m3) | Sand Cement Ratio (kg/m3) | Cement Quantity (kg/m3) | Sand Quantity (kg.m3) | Foam Agent Quantity (lr/m3) | Applications |
---|---|---|---|---|---|
300 350 400 450 | 0:1 0:1 0:1 0:1 | 250 290 330 375 | 1.32 1.28 1.25 1.21 | Thermal Insulation of flat roof with contemporary slope formation, Garrets Insulations, Floor Screeds, Interspace Filling, Grips, Light block for tile, lintol floors for insulations | |
500 550 600 700 800 | 0:1 0:1 0:1 0:1 0:1 | 465 485 515 620 730 | 1:18 1:15 1:11 1:14 1:12 | Light weight curtain wall, blocks for insulation | |
900 1000 | 2:1 2:1 | 280 315 | 560 630 | 1.03 0.96 | Insulation blocks for masonry |
1100 1200 1300 1400 1500 1600 | 2:1 3:1 3:! 3:1 3:1 3:1 | 345 290 310 330 360 380 | 690 860 930 995 1075 1145 | 0.88 0.80 0.72 0.64 0.56 0.48 | Pre-fab insulation panels, for civil and industrial buildings, in-sito vertical casting walls |
Table 1: Foam Concrete Design Mix
Advantages
- Very light material
- Economical
- Incombustible
- Insulating
- Inalterable
How Foam Concrete is being use in Filling
- The Engineer should establish the required height or level of fill by the use of temporary markers or level.
- Once the required level has been established, start filling of foam concrete up to the marked level by aluminium angle to form a smooth and evenly levelled surface.
- The use of machine called “Aerator” which automatically sucks the specified quantity of foaming agent and water mixes them with compressed air to form a foamlike mixture. This will then be poured into concrete mixer that has already cement and water inside. The amount of cement needed is in proportion to the required density in accordance to the Table 1 given above.
- Once the concrete mixer is full, the Aerator is turned off and the concrete mix is then ready to be pour into the floor surface.
- The curing of the screed is about one day by the use of fresh water. It is then be fully dry within two days.
What do you think about this article? Tell us your thoughts! Leave a comment on the section below. Subscribe to our newsletter to be updated with the latest posts or follow us on our social media pages on the below icons.